Barrel finishing is a widely-used mass finishing process that can provide a wide range of finishes for small to medium-sized parts. This process involves placing the components to be finished in a barrel-shaped container along with abrasive media and a liquid finishing compound. The barrel is then rotated at a controlled speed, causing the components and media to tumble and move against each other, resulting in friction and abrasion.
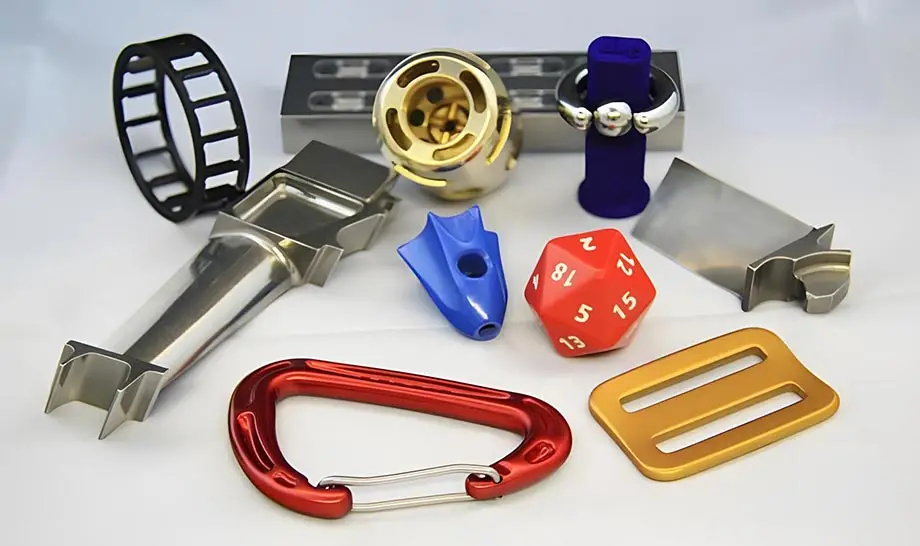
PDJ Vibro Barrel Finishing machines are specifically designed to process small, robust components where an aggressive finishing process is required. Our machines offer a wide spectrum of finishes, including light and heavy deburring, edge breaking, radiusing and the removal of corrosion. The sliding/tumbling action, combined with our machines' process chamber sizes, makes them ideal for a selection of applications. Our process chamber sizes range from 15 litres to 500 litres.
PDJ Vibro's Barrel Finishing machines also come with optional features to customise your finishing process. These features include PLC controls, variable speed control, acoustic suppression covers, vibratory parts/media separation unit, and effluent control.
Barrel finishing is cost-effective, as it can handle large batches of components simultaneously, resulting in reduced labour costs and increased efficiency.
Depending on the specific finishing needs of the components being processed, barrel finishing can use various abrasive media, such as ceramic, plastic, and steel. The type of finishing compound used can also vary, with options such as alkaline or acidic compounds, detergents, and rust inhibitors available.
Overall, barrel finishing is a versatile and efficient finishing method for deburring, polishing, and surface finishing small to medium-sized parts. It is widely used in industries such as automotive, aerospace, and medical device manufacturing in the UK. If you are looking for high-quality barrel finishing equipment or services, PDJ Vibro has the expertise and equipment to meet your needs.
What else to consider:
- Barrel finishing can be dirty at unload due to the process using batches of water and chemicals.
- Media and parts separation can be laborious.
- Process chamber linings commonly last 2-10 years (subject to use).
- Motor bearings will require replacing every 5000 hours.
- Running costs can be calculated after process trials.
To confirm your process requirements why not try our free sampling service
View our range of barrel finishing machines
To discuss your project our experts are ready to help on 01908 648757.