Descaling and deburring as well as superfinishing of motorsport gears are the latest subcontract services being brought in-house. Since the mid-1980s, All Gear Services has been making high quality gears and related products for motorsport gearboxes and commercial applications. A variety of materials is processed, from case hardening steel through stainless steels for marine use to aluminium for pulleys.
Descaling and deburring as well as superfinishing of motorsport gears
are the latest subcontract services being brought in-house.
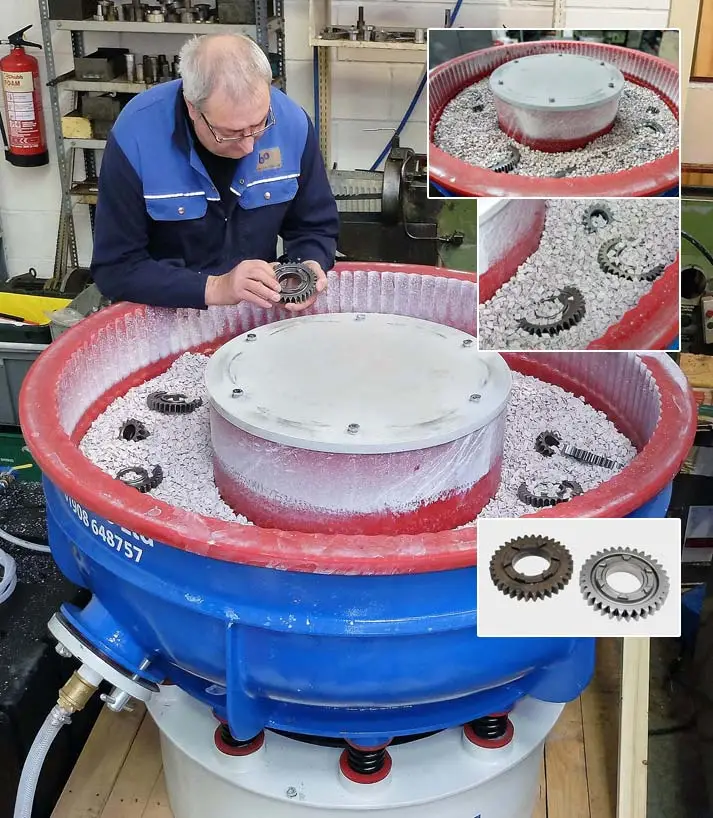
Since the mid-1980s, All Gear Services has been making high quality gears and related products for motorsport gearboxes and commercial applications. A variety of materials is processed, from case hardening steel through stainless steels for marine use to aluminium for pulleys. Small to large batch production is undertaken, from a one-off repair for a broken-down machine to volume manufacture for the motor industry.
As business grew, Steve Cooper and his co-directors found themselves turning and gearcutting in-house but subcontracting out most other work. It included heat treatment, grinding, milling and superfinishing, which polishes gears to reduce vibration, extending the life of a race car gearbox.
The approach to finishing the gears changed at the MACH 2014 machine tool exhibition in Birmingham, when Mr Cooper visited the PDJ Vibro stand and discussed alternative options with one of the directors, Paul Hurley. The meeting was prompted by the demise of an old drum-type rumbler that was used to clean heat-treated steel parts at All Gear Services’ factory in Finchampstead, Berkshire.
Initially, the gears were sent to PDJ Vibro’s technical centre in Bletchley for descaling, deburring and edge breaking in vibratory bowls operated by its subcontract division. This service is a major part of the firm’s business and more than 35 million parts are processed annually, in most cases within in a 24-hour turnaround, for customers that prefer to outsource the function.
Investing in Vibratory Machinery
However, Mr Cooper’s policy was to bring in-house as many processes as feasible, so a 300-litre capacity vibratory bowl finishing machine from PDJ Vibro’s economy range was installed at Finchampstead towards the end of 2014. Filled with a ceramic medium supplied with a recirculating, filtered mixture of water and metal finishing compound, it has reduced processing time from 10 hours in the old rumbler to just four hours and has drastically improved the finish on component surfaces.
Due to the generous size of the vibratory machinery, up to 80 parts can be processed at a time, reducing the previous daily rumbling operations to one or two vibratory processes per week. Around 75 per cent of heat treated components at the Finchampstead factory are finished in this way. Only clutch shafts and drive shafts too long for the bowl are cleaned by hand.
Of the gears and shafts that are not heat treated, accounting for around 40 per cent of production, some are put through the bowl for a shorter period for deburring and surface improvement.
Mr Cooper said, “Stainless steel is a relatively soft material that tends to burr during machining. After putting our components into the vibratory bowl for an hour, the burrs are removed and the surface finish becomes lustrous. The appearance is fantastic and customers frequently comment on how much better the gears look now.
“We could process our aluminium gears in a similar way, but Paul Hurley advises that a change of ceramic medium would be needed. As aluminium is shiny anyway and is often anodised, so far we have opted not to put them in the vibratory bowl.”
A further recommendation from PDJ Vibro is the imminent addition of a switch on the economy bowl that will reverse the toroidal action of the ceramic medium. It will bring the components to the surface after processing, making them easier to remove. A timer will also be fitted to allow finishing to begin in the early hours of the morning so that it is complete when staff arrives for work in the morning.
Superfinishing on the increase
That is only part of the finishing story at All Gear Services, however. Of the components supplied to motorsport customers, which accounts for around half of the company’s business, 60 per cent are currently superfinished. That proportion is increasing as race teams become more aware of the benefits of reducing friction in transmissions, namely increased speed and lower maintenance costs.
Mr Cooper previously sent gears and shafts to a firm specialising in the acid-isotropic superfinishing process. While PDJ Vibro sells new machines that employ the process and offers it in the subcontract department, it tends to be aggressive, eroding metal surfaces and affecting the accuracy of components.
So the company normally recommends the porcelain and paste option for superfinishing, which polishes surfaces efficiently but without removing any discernible amount of metal. Mr Cooper sent sample parts to PDJ Vibro for trial processing using the method and was so impressed that all superfinishing is now done that way in the subcontract department at Bletchley. It is also less expensive than the isotropic method.
Superfinishing will be transferred to Finchampstead during 2015, for which All Gear Services will buy a second, similar 300-litre bowl filled with the requisite media.
The acquisition will complete the rebalancing of production between in-house resource and bought-in subcontract services. The company has for many years used a Hurth hobber and a Sykes shaper to generate straight, helical, bevel and worm gears. They start out as 60 to 220 mm blanks which are turned on a Daewoo (now Doosan) lathe and a new CNC Hurco TM10i acquired last year.
Previously subcontracted milling costing many thousands of pounds each month to produce the dogs on the reverse of gears was also brought in house in 2014 through the purchase of a Hurco VM10i. Grinding will continue to be subcontracted out to GP Precision in Finchampstead and TTI in Luton will remain the preferred supplier for heat treatment.
Related Products