Superfinishing blog
Read the latest news, developments and opinion pieces on our superfinishing from mass finishing specialists PDJ Vibro Ltd.
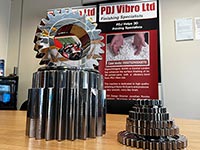
In the fast-paced, high-performance world of the automotive industry, the slightest edge can make all the difference. The finishing process, and in particular superfinishing, can provide that edge. It refines the minutest details of a component's surface, impacting everything from fuel efficiency to the life span of the part. Here at PDJ Vibro, we're at the forefront of this, driving the industry forward with our expertise in superfinishing.
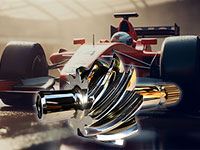
Vibratory superfinishing, such as PDJ Superfinishing, is commonly used on a variety of moving engine parts to improve their surface finish, reduce friction, and increase their longevity. Here are some of the moving engine parts that are commonly superfinished:
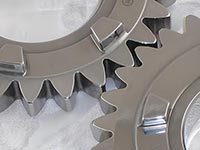
In the world of motorsport, every detail matters. The smallest adjustment can be the difference between winning and losing. One such detail is the surface finish of the components used in the vehicles. In this blog, we delve into the world of PDJ Superfinishing, a process that significantly improves the surface finish of components, and how it's making waves in the motorsport industry.
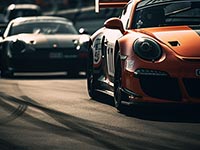
Hey there, speed enthusiast! If you're in the world of motorsports, you know that every millisecond counts. You're always looking for that edge, that secret sauce that can shave a fraction of a second off your time and put you ahead of the pack. That's where vibratory superfinishing comes in.
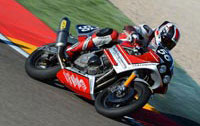
Established in 1989, Nova Racing (www.novaracing.co.uk) is one of the only companies to supply racing gearboxes to the British superbike grids. At its Partridge Green factory in West Sussex, a pair of vibratory bowl finishing machines from PDJ Vibro is employed to polish nearly all of the gears and shafts, after they have been machined and hardened, in a process referred to as superfinishing.

Three new vibratory finishing machines from PDJ Vibro Ltd are helping the Metal Improvement Company (MIC) at its Derby facility to streamline the ‘C.A.S.E™’ isotropic superfinishing process, which uses a combination of controlled shot peening, surface treatment by oxalic acids and non-abrasive vibratory finishing to enhance the fatigue strength and surface properties of components operating under stress and enable them to resist high stress loadings.