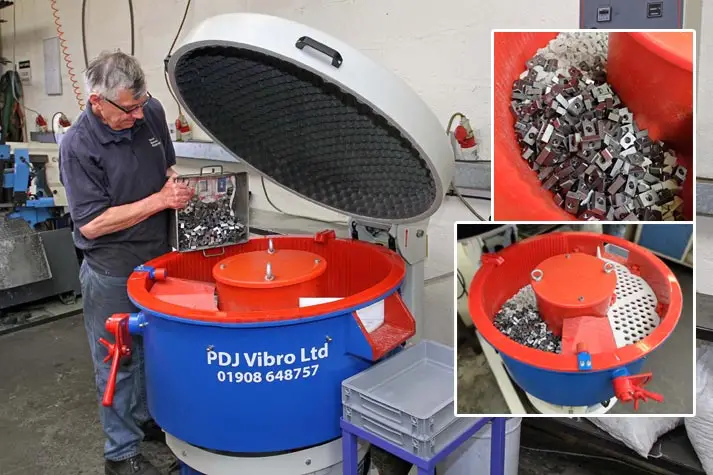
Having installed a 120-litre capacity vibratory finishing bowl from PDJ Vibro in January of this year, Rob Bennett, director of subcontract CNC machinists, Scot Bennett Engineering Limited, decided in May that he had ordered a machine of less than optimal specification. At the outset he had not appreciated the value of having automatic separation of finished components from the abrasive medium when processing is complete.
Mr Bennett said, “I didn’t think there was much that could be done. I had been using the machine for four months, but I thought I would call PDJ Vibro anyway.
“To my surprise, they offered to replace the bowl with a new 120-litre model, but this time fitted with a screen for automatically separating the parts at the end of the cycle. v “It means that our operators do not have to plunge their hands into cold, wet abrasive to extract of the components manually, which is an unpopular job to say the least.”
It is PDJ Vibro’s policy to exchange its finishing equipment within six months of installation, provided that the customer is upgrading the specification and that the vibratory bowl or trough is no larger than 400 litres. Only the difference in price between the two machines is payable.
The company’s managing director, David Hurley commented, “We take responsibility for supplying the right equipment to a customer based on their requirements at the time of order.
“These requirements can change, however. So we are always ready to carry out a review and suggest how a user’s new work or other wishes can be accommodated.
“We pride ourselves on our partnership approach and provide a unique, future-proof service whereby it is virtually impossible for a customer to get it wrong.
“Our subcontract department can even finish components for them if they do not want to purchase equipment at that time, or if an unusually large production run comes along.”
Northampton-based Scot Bennett came across PDJ Vibro towards the end of the 1990s, when the subcontractor received an order that required turning as well as drilling and tapping of 12.7 mm square steel bar. A burr was invariably formed during part-off, so a 30-litre bowl was installed to remove the unwanted metal from the components and at the same time radius the edges.
Rob Bennett continued, “We are now doing a lot more milling and drilling, both on machining centres and on driven-tool lathes, and we find that there is an increasing need for deburring, hence the purchase of the 120-litre bowl. “PDJ Vibro finished some sample components first at their technical centre and showroom in Bletchley to prove that the process worked.
“We have found the supplier to be very helpful and price competitive, so we do not need to go elsewhere for our finishing equipment.”
From 15 to 20 kilograms of components at a time are processed in the bowl, representing anywhere between 20 and 200 components, depending on their size. A ceramic medium of size 6, 10, 20 or 25 mm is used to suit the component shape and complexity.
Cycle time varies from 15 to 30 minutes and an acoustic cover attenuates the transmission of noise to the working environment. A non-foaming detergent containing a corrosion inhibitor is dosed automatically into the recirculating water to clean and brighten the parts.
Related Products