Vibratory cleaning is one function, of many, that our vibratory finishing machines can perform to provide consistent and spotless outcomes. In this guide, we will explore what vibratory cleaning is, where it can be applied and how it can benefit you.
Table of Contents
- What is Vibratory Cleaning?
- Benefits of Vibratory Cleaning
- Applications of Vibratory Cleaning
- How Vibratory Cleaning Works
- Choosing the Right Machine for You
What is Vibratory Cleaning?
Vibratory cleaning is an application of vibratory finishing machines, where mechanical vibrations cause the parts and media in the machine to move and grind against each other, resulting in clean and polished components.
Benefits of Vibratory Cleaning
- Efficient
- Cost-effective
- Versatile
- Consistent
Our vibratory finishing machines will boost your efficiency by quickly cleaning large batches of parts simultaneously, whilst also cutting costs by reducing manual labour. Hand processes are more likely to lead to inconsistency, but with vibratory finishing machines, you can achieve a uniform and clean finish across all parts every time. Vibratory finishing machines are versatile tools, meaning we can find the right media and process to suit your needs.
Applications of Vibratory Cleaning
- Deburr
- Descale
- Polish
- Degrease
Vibratory finishing machines are versatile and can be used to finish a wide variety of materials. Here are some of the common materials that can be processed using vibratory finishing:
Metals:
- Steel (Mild and Stainless): Often used for deburring, polishing, and surface improvement.
- Aluminium: Frequently processed to achieve a smooth, polished finish or to remove burrs.
- Brass and Copper: These softer metals benefit from vibratory finishing for deburring, polishing, and surface treatment.
- Titanium: Used in aerospace and medical applications, titanium can be polished and deburred using vibratory finishing.
- Precious Metals (Gold, Silver): Vibratory finishing is used to polish and finish delicate jewelry pieces and components.
Plastics: Various types of plastics can be processed to remove sharp edges, improve surface finish, or prepare for further processing.
Ceramics: Often used to smooth out surfaces and improve finish quality, particularly in applications like tiles or decorative ceramics.
Composites: Vibratory finishing can help in deburring and polishing composite materials, which are often used in high-performance applications like automotive and aerospace.
Rubber: Certain vibratory finishing processes can be used to deburr and smooth rubber components, particularly those used in industrial applications.
Glass: Some vibratory finishing machines can finish glass, particularly for smoothing edges or polishing surfaces.
Wood: In some cases, vibratory finishing can be used for smoothing and finishing wood products, especially in small-scale applications or where delicate finishing is required.
How Vibratory Cleaning Works
After placing parts into a vibratory bowl, the friction between components and media creates a deburring or cleaning action that can involve polishing, descaling, degreasing, oil removal, and corrosion protection for components, consistently resulting in a clean and smooth finish.
Choosing the Right Machine for You
When choosing a vibratory finishing machine, you have to consider the component’s material, the size, the shape and your desired finish. Our specialists will help you find the right machine for you, we even offer free sample processing so that we can finetune your process before you commit to anything.
Are you ready to improve your cleaning process? Start seeing the benefits of vibratory finishing today! Contact us online or by phone to speak to one of our specialists and receive a personalised quotation to get the best vibratory cleaning solution for your needs.
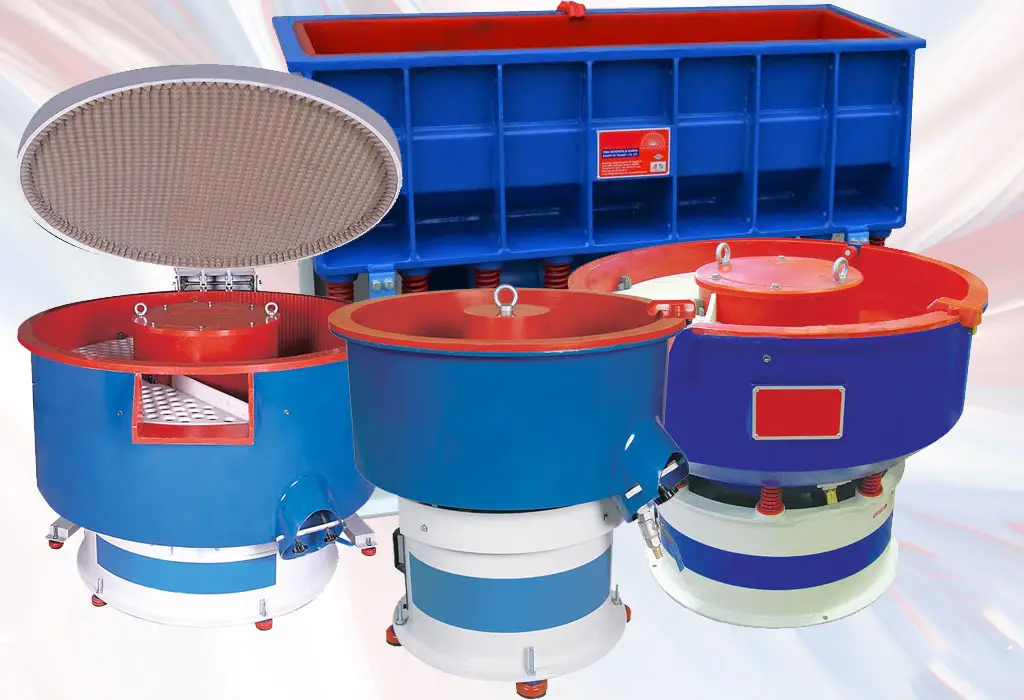
Vibratory cleaning will help you to unlock precision, efficiency and superior quality in your production line. Whether you want to deburr, polish, or achieve the perfect finish, our vibratory machines can help you achieve it. Explore our range of machines and contact us to find out how to achieve consistently great finishes on your components