At PDJ Vibro, we prioritise using super-thick linings in our equipment. Still, as the market witnesses an unprecedented surge in polyurethane costs, consumers may be tempted to choose thin 16mm linings as a cost-cutting measure. However, we strongly advise against this. Opting for subpar linings can result in onerous premature maintenance costs, amounting to thousands of pounds, as well as extended periods of downtime.
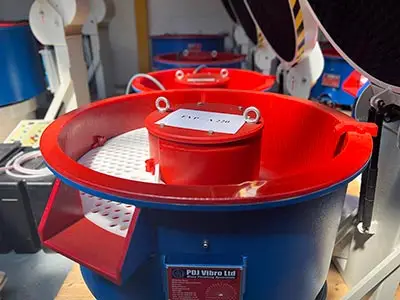
At PDJ Vibro, we prioritise using super-thick linings in our equipment. Still, as the market witnesses an unprecedented surge in polyurethane costs, consumers may be tempted to choose thin 16mm linings as a cost-cutting measure. However, we strongly advise against this. Opting for subpar linings can result in onerous premature maintenance costs, amounting to thousands of pounds, as well as extended periods of downtime. This article will delve into why we believe in the importance of super-thick linings and outline the potential pitfalls of choosing thinner alternatives.
The Significance of Super Thick Linings
Unparalleled Durability and Longevity
PDJ Vibro firmly believes that investing in super-thick linings for vibratory finishing machines is the superior choice due to their unmatched durability and longevity. These linings are specifically engineered to withstand the rigorous demands of industrial applications, including the constant movement of abrasive materials. Thick linings provide a robust barrier that protects the equipment from wear and tear, significantly reducing the need for premature repairs and replacements.
Minimised Maintenance Costs
Thin linings may appear attractive initially due to lower upfront costs, but they often prove more expensive in the long run through high maintenance costs. Thin linings wear down quickly, leaving the underlying equipment vulnerable to damage. Consequently, operators are burdened with frequent maintenance and repair expenses, accumulating into thousands of pounds. Instead, choosing super thick linings can help to alleviate these financial burdens and ensure a more cost-effective solution.
Reduced Downtime and Increased Productivity
Thin linings are prone to premature failure, necessitating unscheduled downtime for repairs. At PDJ Vibro, we recognise that prolonged equipment downtime can severely hamper our customers' productivity and profitability. On the other hand, super thick linings offer extended service life and enhanced resistance to wear and abrasion, resulting in reduced inactivity and uninterrupted operations. Investing in reliable, long-lasting linings enables our customers to maximise productivity and maintain a competitive edge in their respective industries.
Enhanced Performance and Consistency
Vibratory finishing machines rely on consistent and precise performance to deliver optimal results. Thin linings are more susceptible to uneven wear, leading to fluctuations in performance and subpar finishing quality. In contrast, our preferred super-thick linings provide a stable and reliable surface that ensures consistent results over an extended period. By prioritising performance and quality, we aim to provide our customers with a superior finishing experience.
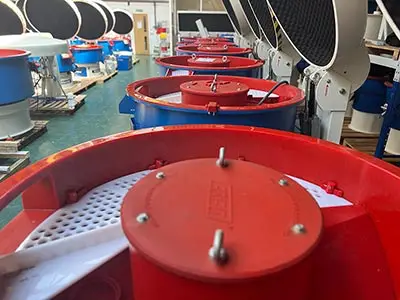
At a time when polyurethane costs have skyrocketed, we at PDJ Vibro stand firm in our commitment to super-thick linings for our vibratory finishing machines. We recognise the benefits of super-thick linings, including durability, minimised maintenance costs, reduced downtime, and enhanced performance, to deliver exceptional value to our customers. While cost-cutting measures may be tempting, we want our customers to understand the potential issues with choosing thin linings. For example, premature maintenance costs that run into thousands of pounds and extended periods of downtime can far outweigh the short-term savings. To avoid such issues, we strongly recommend super thick linings to ensure our customers can achieve optimal results, cost efficiency and maximum productivity.