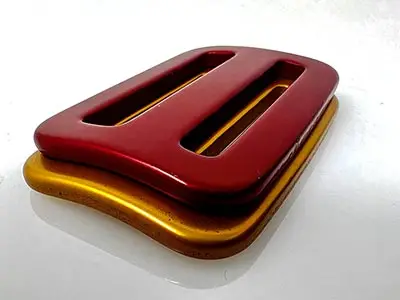
Safety is an inherent concern when it comes to motor vehicles and climbing gear. One integral yet often overlooked component that significantly contributes to safety is the safety buckle. These unassuming elements play a pivotal role in securely fastening straps and harnesses, thereby preventing potential accidents and injuries. However, the often-underestimated radiused edge of safety buckles holds paramount importance. This article dives into the significance of safety buckles, the critical nature of achieving a perfect radiused edge, and how advanced finishing techniques—vibratory, barrel, and centrifugal—supported by PDJ Vibro, can ensure optimal safety.
Understanding the Radiused Edge's Significance
The radiused edge of a safety buckle might seem like a minor detail, but it has profound implications for safety and functionality. A smooth, rounded edge offers numerous benefits that contribute to the overall safety of the buckle. Firstly, it minimizes the risk of abrasions and cuts, which is especially critical for climbing gear and motor vehicle harnesses. Friction against the skin or surfaces can lead to potential injuries, making a radiused edge crucial.
Additionally, the radiused edge prevents materials from fraying or deteriorating over time. This is particularly crucial for climbing gear, where abrasions or frayed edges could compromise the equipment's integrity, putting climbers at risk. In the context of motor vehicles, safety buckles with well-crafted radiused edges are less likely to damage straps, extending the equipment's lifespan.
The Art of Achieving the Radiused Edge: Vibratory, Barrel, and Centrifugal Finishing
Achieving the perfect radiused edge requires precision and specialized techniques. Vibratory, barrel, and centrifugal finishing are three advanced methods that excel in this domain.
Vibratory Finishing: In this method, safety buckles are placed in a vibratory container alongside finishing media. The vibrations cause the media to interact with the buckles, leading to the desired radiused edge. Vibratory finishing is particularly suited for intricate components, ensuring uniform and consistent results.
Barrel Finishing: Similar to vibratory finishing, barrel finishing involves placing buckles in a rotating barrel with finishing media. The tumbling motion within the barrel generates friction and abrasion, effectively creating the radiused edge. This method is adaptable for a range of safety buckle shapes and sizes.
Centrifugal Finishing: Centrifugal finishing requires safety buckles to be placed in a rotating container. The centrifugal force propels the buckles against the media, resulting in the desired radiused edge. This technique is particularly effective for achieving a uniform finish on complex or curved components.
PDJ Vibro: Elevating Safety Buckle Finishing
In the pursuit of ensuring safety buckle excellence, partnering with the right experts and resources is paramount. PDJ Vibro, a reputable provider in the field, offers an all-encompassing solution for achieving optimal radiused edges. They offer state-of-the-art finishing machinery, consumables, and a finishing service that caters to the intricate needs of safety buckle production.
What truly sets PDJ Vibro apart is their team of seasoned experts, armed with decades of practical experience. These professionals understand the nuances of safety buckle finishing and guide clients through each stage of the process. From selecting the most suitable finishing technique to refining the process for impeccable results, PDJ Vibro's experts ensure that safety buckles meet the highest standards of quality and safety.
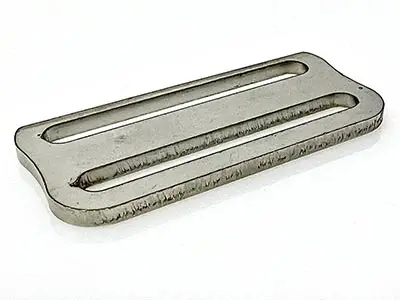
Conclusion
In the realm of both motor vehicles and climbing gear, safety is paramount. The seemingly small radiused edge of safety buckles holds significant weight in preventing injuries and extending equipment lifespan. Advanced finishing techniques—vibratory, barrel, and centrifugal—emerge as the heroes in achieving the perfect radiused edge. With the backing of PDJ Vibro's cutting-edge machinery, consumables, and expert guidance, attaining an impeccable radiused edge becomes a seamless process. The result is enhanced safety, reliability, and peace of mind for those who rely on these vital safety components.