Table of Contents
- Introduction
- Understanding the Vibro Polishing Process
- Vibro Polishing for 3D Printed Parts
- Technical Centre Consultancy
- Subcontract Vibro Finishing Service
- Low-Cost Vibro Bowls
- Conclusion
Introduction
The humble vibratory polishing machine, often tucked away in a factory's corner, holds immense potential in improving manufacturing processes. While it might be one of the least likely machines to be replaced until it collapses, there's much more to vibro polishing than meets the eye. This post looks into the key considerations for getting rid of hand polishing, automating the finishing function and the benefits of the vibro polishing process.
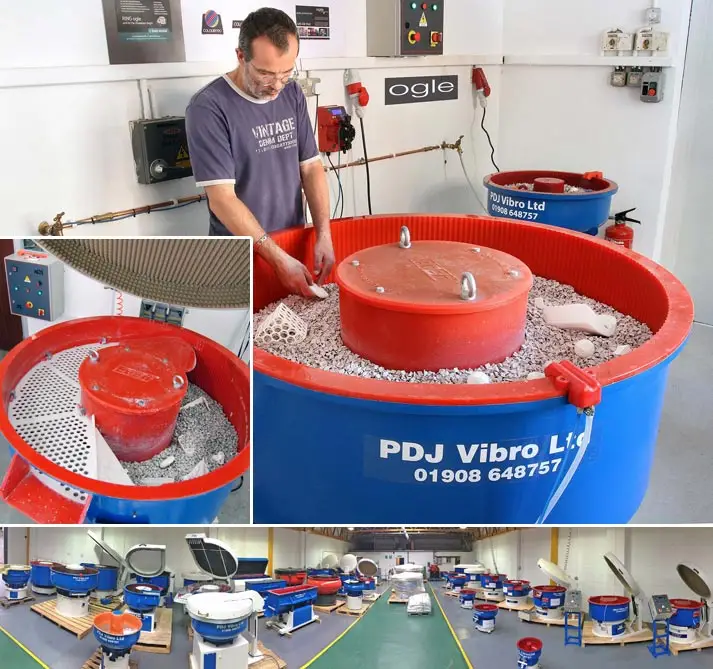
Understanding the Vibro Polishing Process
PDJ Vibro uses its extensive experience to guide manufacturers in automating their finishing functions. Whether a customer is investing for health and safety reasons or to improve consistency of finish, PDJ Vibro offers unrivalled consultancy services. With over 100 years of combined industry experience, the company covers everything from;
- Deburring
- Edge breaking
- Radiusing
- Superfinishing
- Degreasing
- Drying
to pretreatment for anodising, chemical blacking, or painting.
Vibro Polishing for 3D Printed Parts
When a company specialising in metal cutting decides to add additive manufacturing (AM) to its capabilities, understanding the vibro polishing process becomes crucial. PDJ Vibro's experience with customers like 3D Printing Bureau highlights key considerations for finishing 3D printed components. Choosing the right size and shape of ceramic abrasive is vital to avoid media becoming lodged in small spaces. Larger media are preferable for external surfaces to prevent embedding inside the component.
The vibro polishing process also rounds sharp edges, so parts with thin edge detail may not be suitable for this method. However, PDJ Vibro bowls excel at smoothing flat surfaces and areas of gradual curvature, creating a satin-like finish. The process is particularly beneficial for plastic parts, which become more flexible after vibratory finishing, absorbing water to replace the moisture lost during laser sintering. Vibro polishing reduces the lead time for preparing 3D printed items for painting by one-third compared to hand finishing, freeing up skilled operatives for other tasks and enhancing customer service.
Technical Centre Consultancy
PDJ Vibro's problem-solving expertise extends beyond equipment selection. At its technical centre in Bletchley, visitors can see over 120 new and used machines ready for ex-stock delivery, with part-exchange options available. The centre holds more than 70 tonnes of consumables, including ceramic and porcelain media, superfinishing compounds, liquid detergents, and chemicals. Customers often bring in sample components for free trials to see the vibro process in action. Factors considered include the number of parts per batch, production frequency, drainage and noise issues, component size, and vulnerability to impingement damage.
Subcontract Vibro Finishing Service
PDJ Vibro also offers a 24/7 subcontract vibro finishing service, ideal for manufacturers facing temporary capacity bottlenecks or preferring not to undertake on-site finishing. At PDJ we can typically turn around component batches within 24 hours. Upgrades to existing vibratory equipment can address changing applications. Needs such as automatic component separation, retrofitting acoustic covers, or swapping machines for larger models to increase throughput are all part of PDJ Vibro's comprehensive service.
Low-Cost Vibro Bowls
Complementing its high-end offerings, PDJ Vibro's range of competitively priced vibro bowls includes models with process chamber capacities of 300, 150, and 75 litres. These economy models, built to high specifications with durable, stress-relieved bowls and cast polyurethane linings, cater to low-volume, intermittent finishing applications. Options include PLC control of additive dosing, water metering, and recirculation, as well as effluent control, automatic parts separation, and acoustic suppression.
Conclusion
PDJ Vibro's extensive experience and comprehensive range of vibro polishing and deburring solutions make us a valuable partner for manufacturers looking to enhance their finishing processes. Whether you're interested in automating your finishing function or exploring cost-effective equipment options, PDJ Vibro offers the expertise and resources to meet your needs.
Related Products