PDJ Vibro Blog
Read the latest news, developments and views from mass finishing specialists PDJ Vibro.
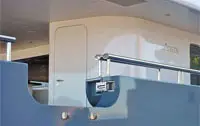
Family-run subcontract machinists, Mathison Engineering, specialises in producing 316 stainless steel marine fittings in quantities ranging from one-off prototypes to high volume runs. Accounting for around 80 per cent of turnover, the products are to be found in vessels all over the world, but mainly around the coasts of Europe, the US and Iceland.
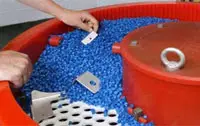
When global materials engineering company Morgan Advanced Materials needed a new vibratory finishing bowl, the company turned to PDJ Vibro for a solution. Morgan manufactures high specification, technically complex components for a wide range of applications, from military to medical, transportation and petrochemical.
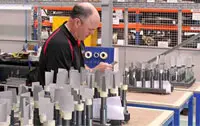
Vibratory cleaning and surface preparation brought in-house, together with engine test, in major investment programme. A £1 million expansion of activities at the Lincoln works of Turbine Efficiency has seen the installation of two stands for testing powergen gas turbines after they have been stripped down, repaired and rebuilt.
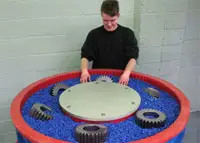
To complement its high-end vibratory finishing and polishing bowls, a new range of three competitively priced models were unveiled by PDJ Vibro at the last MACH Exhibition. With process chamber capacities of 300, 150 and 75 litres, the machines are priced about 25 per cent lower than the company's existing bowls. Nevertheless, the new models are built to a high specification. They have a durable, stress relieved bowl with cast polyurethane lining, driven by a heavy-duty, three-phase electric motor.
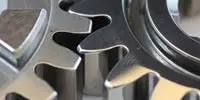
Mass finishing is increasingly becoming the best way to finish components confining hand finishing to the history books. Vibratory finishing is a mass finishing process used to burnish, deburr, clean, radius, de-flash, remove rust, brighten, surface harden, surface improve and edge break.
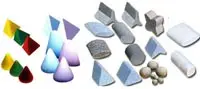
Quality of finish – Probably the most important question; what quality of metal surface finishing do you need to ensure your product meets its technical requirements? Parts for the construction industry may not need to be finished to 0.03Ra but parts for Formula 1 do. Are you doing enough to keep your contract?
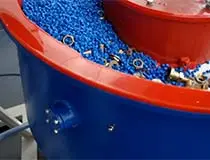
While at first glance vibratory deburring may seem somewhat a niche market it should be noted that even an enormous range of mass produced metal, plastic and even (in some cases) wooden components require deburring. The UK has been the home of vibratory deburring. These machines are also a standard solution for the manufacturing community internationally.
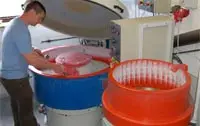
"The vibratory and centrifugal finishing processes are new to us and even though we carried out thorough practical trials with PDJ before we introduced the machines, there was still some scepticism here about the extent of their capabilities as surface finishing tools for the type of work we undertake. I’m glad to say that practice has demonstrated that the scepticism was unfounded."
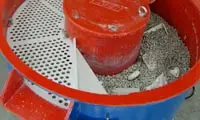
Selective Laser Sintering (SLS) specialist – 3T RPD Ltd, based in Newbury – has recently installed a vibratory finishing machine from PDJ Vibro, to complement its surface finishing capability.
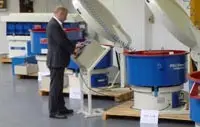
Leading vibratory finishing and component polishing specialist, PDJ Vibro Ltd, has recently expanded its warehouse, demonstration and subcontract centre in Milton Keynes. The facility features what the company claims is the UK’s most comprehensive range of new and refurbished vibratory, barrel and centrifugal surface finishing equipment – with more than 120 machines and around 70,000kg of abrasive media in stock.
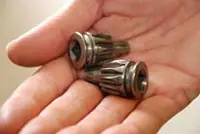
PDJ Vibro machine enhances surface quality of woodworking lathe components. The small town of Axminster in Devon, perhaps best known as a major carpet manufacturing centre, is also the location of Axminster Tool Centre Ltd – the UK's largest supplier of tools and associated equipment and consumables for the woodworker, carpenter and craftsman, many trade professionals and, increasingly, the metalworking specialist.
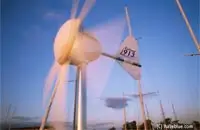
Marine wind turbines are particularly susceptible to corrosion as a result of widely variable weather conditions and constant salt-spray. Their surface finish obviously has to be tough enough to cope with this environment and ensure a maximum working life.
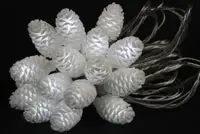
One of the UK’s leading specialists in 3D printing – Central London based, Digits2Widgets – has enhanced its range of surface finishing services with the recent installation of a vibratory finishing machine from PDJ Vibro Ltd. The new machine is dedicated to the high quality polishing of Nylon SLS parts and produces a very smooth, ivory-like finish.
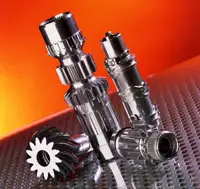
Three new vibratory finishing machines from PDJ Vibro Ltd are helping the Metal Improvement Company (MIC) at its Derby facility to streamline the ‘C.A.S.E™’ isotropic superfinishing process, which uses a combination of controlled shot peening, surface treatment by oxalic acids and non-abrasive vibratory finishing to enhance the fatigue strength and surface properties of components operating under stress and enable them to resist high stress loadings.
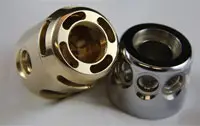
With over 80 years of experience in the vibratory finishing business, PDJ Vibro are leaders in the metal finishing industry. That means we understand that, in manufacturing and production, capacity planning is not always an exact science and making decisions about equipment investment may not be straightforward. That’s why PDJ Vibro offer a unique no quibble 30 day money back guarantee.
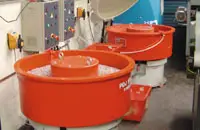
Well-established precision engineering firm, Dowse Engineering Ltd, based in Bletchley, Milton Keynes, boasts an excellent reputation amongst its prestigious customer base, which includes companies in motor racing, medical technology, aerospace, and the photographic and telecommunications sectors.
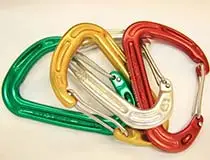
One of the UK’s leading anodising and plating specialists – Anodisers Runcorn Ltd – has eliminated the labour-intensive task of manually deburring and removing inclusions and minor surface defects from mainly aluminium and copper components, following the installation of a new vibratory finishing machine from PDJ Vibro Ltd.