As the field of 3D printing continues to evolve, so too do the methods for finishing these carefully crafted components. Two of the most commonly used processes are blasting and vibratory finishing. Both are highly effective for deburring and polishing 3D printed parts, but they come with their own unique set of pros and cons. In this blog post, we will dive into the advantages and disadvantages of each, and why vibratory finishing might just be the superior choice.
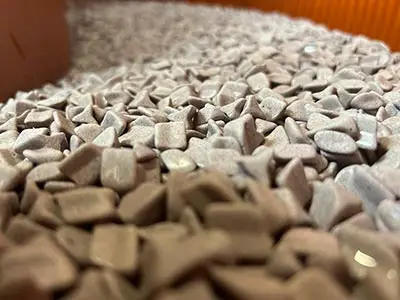
Blasting: Powerful But Not Without Its Challenges
Blasting, often utilised as an impact finishing process, is a high-energy method that uses a stream of abrasive material to smooth and polish the surface of a 3D printed part. It's a powerful process, capable of removing burrs and other imperfections with considerable effectiveness. However, it's not without its drawbacks.
One of the major cons of blasting is the high level of labour involved. Each part needs to be individually blasted, requiring a significant investment of time and effort. This can also result in inconsistent finishes, as the blasting process relies heavily on the skill and attention of the operator.
Furthermore, the running costs of blast cabinets can be high. They regularly need replacement parts and maintenance, which can quickly add up over time. This makes them less cost-effective in the long run, particularly for businesses that have a high throughput of parts needing finishing.
Vibratory Finishing: A Gentle, More Efficient Alternative
In contrast to blasting, vibratory finishing is a far gentler process. As the name suggests, it uses vibration to create a consistent grinding action that efficiently deburrs and polishes 3D printed parts.
One of the key advantages of vibratory finishing is its lower labour intensity. Once the parts are loaded into the machine, the process is largely automated. This means that you can effectively 'set and forget', allowing you to focus on more meaningful tasks – or perhaps just enjoy a well-deserved cup of tea!
In addition, vibratory finishing machines generally require less maintenance than blast cabinets. This is primarily because they don't have the same wear and tear on parts as blasting machines do. They're also more energy-efficient, further contributing to lower running costs.
Moreover, the nature of vibratory finishing ensures a more uniform finish, regardless of the complexity or intricacy of the part. This makes it an ideal choice for 3D printed parts, which often have complex geometries that can be difficult to finish evenly with other methods.
The Verdict: Vibratory Finishing's Gentle Efficiency Wins Out
While both blasting and vibratory finishing have their merits, the latter stands out as the superior choice for deburring and polishing 3D printed parts. The reduced labour intensity, lower running and maintenance costs, and more consistent finishes make vibratory finishing an excellent alternative to blasting.
Whether you're a small business owner looking to streamline your finishing processes, or a hobbyist seeking the best finish for your 3D printed creations, vibratory finishing provides an efficient, cost-effective, and gentle solution. And the best part? You can enjoy that cup of tea while your vibratory finisher does all the hard work for you.