Vibratory Finishing Equipment Blog
Read the latest news, developments and opinion pieces on our vibratory finishing equipment from mass finishing specialists PDJ Vibro.
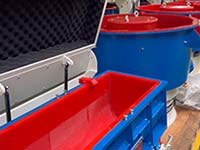
This article discusses some important differences that the circular bowl and rectangular trough vibratory finishing machines have from one another. Each machine has a very special job in the finishing process, and knowing the subtle differences will be of great help in your choice of equipment for what you need.
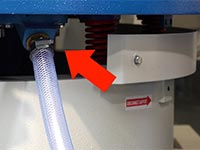
Are you encountering problems with your vibratory finishing process? We're here to help! In our comprehensive 3-minute video, our experts discuss the most common vibratory finishing challenges and reveal how to address them with straightforward maintenance techniques.
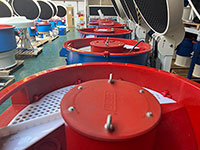
Manufacturing, at its core, is a meticulous balance of processes, all aimed at achieving a high-quality product in the shortest time possible. However, in every manufacturing chain, there are often critical points or bottlenecks that can slow down production, leading to increased costs and delivery times. One such commonly experienced bottleneck is the finishing process.
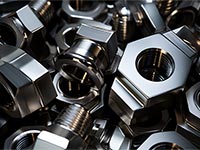
Retaining top talent in any industry is paramount to the success and continuity of a business. In manufacturing, this becomes particularly pertinent when we consider the value added by a trusted team member to the entire process. These individuals often hold intricate knowledge, are adept at handling parts that have undergone the most sophisticated aspects of your production line, and are pivotal in ensuring the end product's quality and consistency.
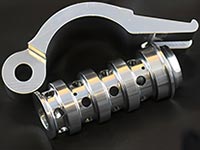
In the manufacturing world, precision is key. Every detail, no matter how minute, can make the difference between a subpar product and one that meets or exceeds expectations. One such detail is the process of hand deburring and polishing. This task, while seemingly mundane, is pivotal for ensuring the smoothness, safety, and functionality of many products. However, there's a certain irony to this process. Here's why:
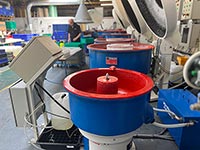
In manufacturing, precision and consistency are the hallmarks of excellence. Yet, when it comes to hand finishing, a task that is inherently human and dependent on individual skill and attention, we encounter the idiosyncrasies that machines don't possess. One of the most frequently referenced examples of this is the "Monday morning and Friday afternoon" issue.
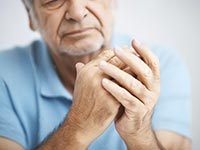
Greetings to my fellow engineers and safety-conscious readers. I've dedicated much of my life to the engineering world, mainly focusing on offering solutions that prioritise efficiency and safety. Today, I'd like to address a less-discussed but pivotal issue in the engineering domain: vibration risks.
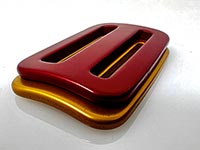
Safety is an inherent concern when it comes to motor vehicles and climbing gear. One integral yet often overlooked component that significantly contributes to safety is the safety buckle. These unassuming elements play a pivotal role in securely fastening straps and harnesses, thereby preventing potential accidents and injuries. However, the often-underestimated radiused edge of safety buckles holds paramount importance...
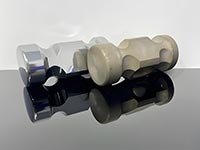
As the Managing Director of PDJ Vibro, I've had the privilege of witnessing firsthand the transformative power of vibratory finishing. This process, often overlooked in the broader manufacturing industry, is a cornerstone of our operations, enabling us to take heat-treated metal components from a raw, unrefined state to a polished, jewellery-like finish.
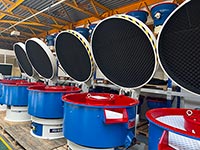
At PDJ Vibro, safety is not just a priority; it's a fundamental principle ingrained in every aspect of our products. One shining example of our commitment to safety is our range of acoustic covers. These covers are meticulously designed and equipped with cutting-edge features to provide a secure and reliable solution for protecting equipment and ensuring the well-being of individuals. Let's delve into why our acoustic covers stand out in terms of safety and how they set the benchmark for the industry.
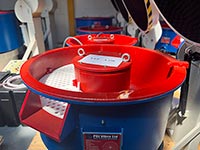
At PDJ Vibro, we prioritise using super-thick linings in our equipment. Still, as the market witnesses an unprecedented surge in polyurethane costs, consumers may be tempted to choose thin 16mm linings as a cost-cutting measure. However, we strongly advise against this. Opting for subpar linings can result in onerous premature maintenance costs, amounting to thousands of pounds, as well as extended periods of downtime.
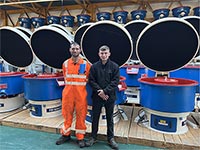
The lovely Guy Martin, off the telly, has been a customer for many years using our same or next day polishing and super finishing service. He recently decided to bring the process in house with a machine and consumables. Adam had the pleasure of guiding Guy through the purchase - a true gentleman and an absolute pleasure to deal with.
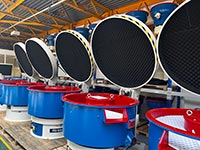
At PDJ Vibro, we are a leading supplier of vibratory, barrel, and centrifugal finishing machines. We have long been recognised for our commitment to maintaining a vast inventory of machines and consumables.
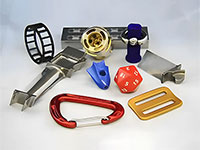
In the world of component manufacturing, perception often translates into reality. The look, feel, and finish of a product can significantly influence its perceived value. A well-finished component not only looks good but also feels good to the touch, thereby enhancing the overall user experience. This is where PDJ Vibro Finishing Systems come into play.

When it comes to component finishing, PDJ Vibro understands that it is often the final stage of a project, but its significance should not be underestimated. As a business partner, we pride ourselves on offering a wide range of benefits that make us the right choice for your component finishing needs. With stocks of 120+ machines and 240 tonnes of consumables, we ensure unmatched reliability, flexibility, and expertise. Let's explore the advantages of partnering with PDJ Vibro.
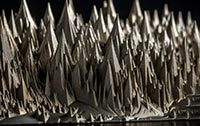
When you look at a metal part under a microscope, what you might initially perceive as a flat surface can quickly resemble a rugged mountain range. Peaks and valleys, invisible to the naked eye, create a terrain that can significantly impact a part's performance, appearance, and readiness for further processing.
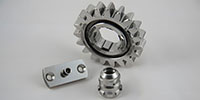
As manufacturers, we constantly strive to optimize our processes for efficiency and quality. A critical part of that equation is the finishing process, which includes deburring, edge breaking, and radiusing.
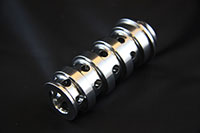
Vibratory finishing is a popular method that can achieve a range of finishes for your parts, from deburring to polishing and radiusing. The decision between subcontracting this process or investing in vibratory finishing equipment can be a difficult one, as each option has its own set of pros & cons.

Maximizing the efficiency of your part processing starts with choosing the right finishing equipment. At PDJ Vibro, we have the expertise and equipment to help you reach your production goals.
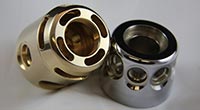
Accelerating part processing is a key concern for many manufacturers, as quicker production leads to increased productivity and profitability. Automated vibratory finishing provides an outstanding solution for those looking to improve their processing speed and efficiency.