PDJ Vibro Blog
Read the latest news, developments and views from mass finishing specialists PDJ Vibro.
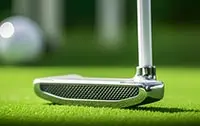
In the ever-changing industrial technology landscape, we must be wary of the "Emperor's New Clothes" phenomenon. This term, derived from a classic Hans Christian Andersen tale, refers to situations where people are led to believe that something is more than it really is, often due to social pressure or misleading claims.

As the field of 3D printing continues to evolve, so too do the methods for finishing these carefully crafted components. Two of the most commonly used processes are blasting and vibratory finishing. Both are highly effective for deburring and polishing 3D printed parts, but they come with their own unique set of pros and cons.
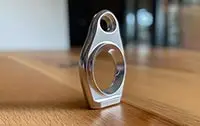
In the ever-progressing world of 3D printing, the finish quality is just as significant as the printing process itself. Amidst a host of finishing techniques, vibratory finishing stands out due to its adaptability and broad-based applicability. Nonetheless, it's important to acknowledge that while it excels in various areas, it does encounter certain limitations.

PDJ Vibro systems are ideal for the post-processing of 3D printed parts due to a multitude of reasons, including their cost-effectiveness and labour efficiency:
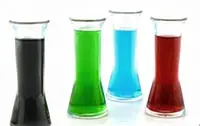
PDJ Vibro's revolutionary new compound, NF-15 XP, has taken the world of 3D printed metals by storm. Designed to enhance the finishing process, NF-15 XP delivers unparalleled results, boasting brighter and more vibrant finishes than ever before. This cutting-edge finishing compound represents a significant leap forward in metal finishing technology.
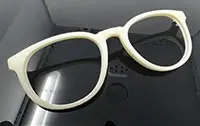
Post-processing of SLS (Selective Laser Sintering) 3D printed parts is essential to achieve a better surface finish. Vibratory finishing is a technique that can be employed to enhance the surface quality of SLS printed components. Let's delve into how vibratory finishing can improve the surface finish of SLS 3D printed parts.
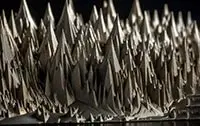
When you look at a metal part under a microscope, what you might initially perceive as a flat surface can quickly resemble a rugged mountain range. Peaks and valleys, invisible to the naked eye, create a terrain that can significantly impact a part's performance, appearance, and readiness for further processing.
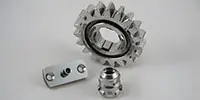
As manufacturers, we constantly strive to optimize our processes for efficiency and quality. A critical part of that equation is the finishing process, which includes deburring, edge breaking, and radiusing.
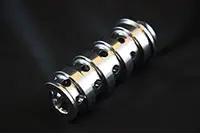
Vibratory finishing is a popular method that can achieve a range of finishes for your parts, from deburring to polishing and radiusing. The decision between subcontracting this process or investing in vibratory finishing equipment can be a difficult one, as each option has its own set of pros & cons.
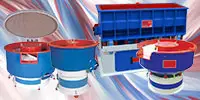
Maximizing the efficiency of your part processing starts with choosing the right finishing equipment. At PDJ Vibro, we have the expertise and equipment to help you reach your production goals.
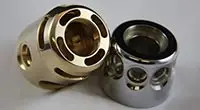
Accelerating part processing is a key concern for many manufacturers, as quicker production leads to increased productivity and profitability. Automated vibratory finishing provides an outstanding solution for those looking to improve their processing speed and efficiency.

Are you tired of worrying about the costs and staffing challenges associated with hand finishing components in your manufacturing process? Let us help you see how much you can save!
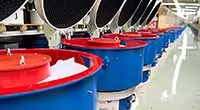
As a business owner, you understand the huge difficulties of finding reliable and skilled staff to handle hand finishing processes. PDJ Vibro has a solution that can change the way you process your parts completely.
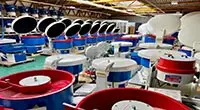
Hand finishing parts has been a staple in the manufacturing industry for decades, but as technology advances and efficiency becomes more important, the use of automated vibratory finishing machines has become a game changer.
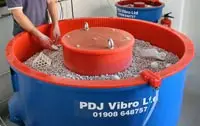
Immediately inside the visitors' entrance to Surface World Live , family-owned vibratory finishing specialist PDJ Vibro promoted its comprehensive range of new and refurbished bowls, barrels and high energy centrifugal equipment, as well as the vast range of consumables on offer.
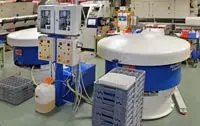
Galvanometers for laser beam steering and scanning in surgical, analytical and other applications include a precision-machined housing in which the stator moves. At the Poole factory of Westwind Air Bearings, which manufactures galvanometer components for its US parent group, Novanta, these coil housings are CNC turned from mild steel bar to within grinding tolerances.
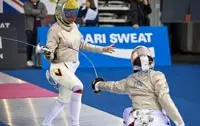
Many fencers around the world including winners at last year’s Olympic Games in Rio use weapons manufactured by London firm, Leon Paul Equipment. What many of them may not realise is the level of expertise that goes into ensuring that the foils, epees and sabres are finished to a very high standard.
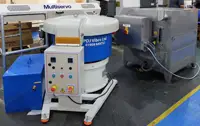
Peterborough subcontractor Westcombe Engineering has installed a new manufacturing cell to produce increased quantities of a family of aluminium engine components for Perkins Engines. It comprises a Haas ST-30 CNC lathe with short bar feeder, a Blast Wash top-loading washing machine and a vibratory bowl finishing machine from PDJ Vibro, the second to be installed in the factory.
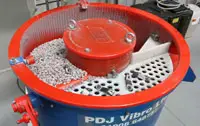
Leading vibratory finishing specialist PDJ Vibro promoted its comprehensive range of new and refurbished bowls, barrels and high energy centrifugal equipment, as well as the vast range of consumables on offer and the company’s repair and subcontract finishing services.
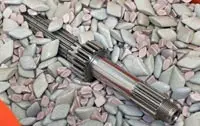
PDJ Vibro will present the two sides of its business at Advanced Engineering UK. One is its new and used finishing machine sales activities and the other is its contract finishing service. Both are designed to make life simpler for manufacturers that want to minimise manual work and move towards automating the finishing process for health and safety reasons and to improve consistency.
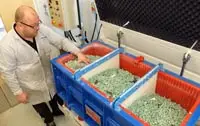
High-end manufacturing solutions for the aerospace engineering sector are provided by Bowmill Engineering from several factory units on the Nuffield Industrial Estate in Poole. In the finishing and assembly department, machined parts are deburred carefully using a variety of finishing practices. In April 2016, the company decided to augment these by installing a PDJ Vibro EVT-320 vibratory trough alongside its existing vibratory bowl machine, which was at full capacity.
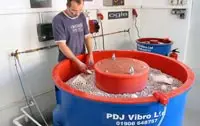
The humble vibratory polishing machine, often tucked away in a factory's corner, holds immense potential in improving manufacturing processes. While it might be one of the least likely machines to be replaced until it collapses, there's much more to vibro polishing than meets the eye. This post looks into the key considerations for getting rid of hand polishing, automating the finishing function and the benefits of the vibro polishing process.
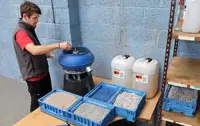
30% reduction in scrap leads to 3-month payback on vibratory bowl. Post Brexit, UK manufacturers will be cultivating more and more business from outside Europe. One subcontractor that already exports one-third of its output, nearly half to China plus some to the USA and Canada, is Stroud-based Truturn Precision Engineering.
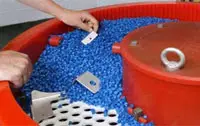
Factories with metalcutting machines invariably use vibratory finishing equipment to remove burrs and sharp edges from components. If parts have been laser-cut from sheet metal, however, deburring and surface enhancement are sometimes secondary. The main purpose of the rumbling action can be to stress-relieve case hardening in the heat-affected zone (HAZ) around the component edges.

Winning a contract to machine large batches of two aileron parts from solid aluminium for the Airbus A320 presented Gloucestershire subcontractor, Norman Precision, with the problem of how to finish the complex components economically, as they require a large amount of hand deburring. The solution was the purchase of a PDJ Vibro 60-litre, bench-top vibratory finishing bowl...
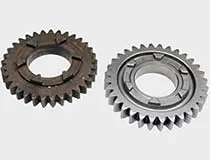
Descaling and deburring as well as superfinishing of motorsport gears are the latest subcontract services being brought in-house. Since the mid-1980s, All Gear Services has been making high quality gears and related products for motorsport gearboxes and commercial applications. A variety of materials is processed, from case hardening steel through stainless steels for marine use to aluminium for pulleys.
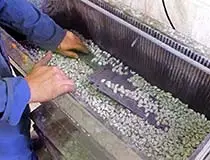
Braintree subcontractor, J Reeves Engineering, which specialises in machining and fabricating components and assembles from sheet metal and tube, took delivery of a vibratory trough deburring machine from PDJ Vibro. It joins a twin vibratory bowl finishing and drying system from the same supplier that has given reliable service for more than 20 years.
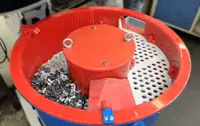
Having installed a 120-litre capacity vibratory finishing bowl from PDJ Vibro in January of this year, Rob Bennett, director of subcontract CNC machinists, Scot Bennett Engineering Limited, decided in May that he had ordered a machine of less than optimal specification. At the outset he had not appreciated the value of having automatic separation of finished components from the abrasive medium when processing is complete.
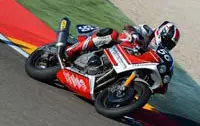
Established in 1989, Nova Racing (www.novaracing.co.uk) is one of the only companies to supply racing gearboxes to the British superbike grids. At its Partridge Green factory in West Sussex, a pair of vibratory bowl finishing machines from PDJ Vibro is employed to polish nearly all of the gears and shafts, after they have been machined and hardened, in a process referred to as superfinishing.
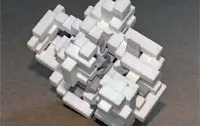
Preparation time for painting plastic components cut by one-third
To assist companies that are considering finishing 3D printed parts automatically using vibratory bowls, guidelines have been prepared by Ogle Models and Prototypes, a leading design and model making bureau based in Letchworth, Hertfordshire.